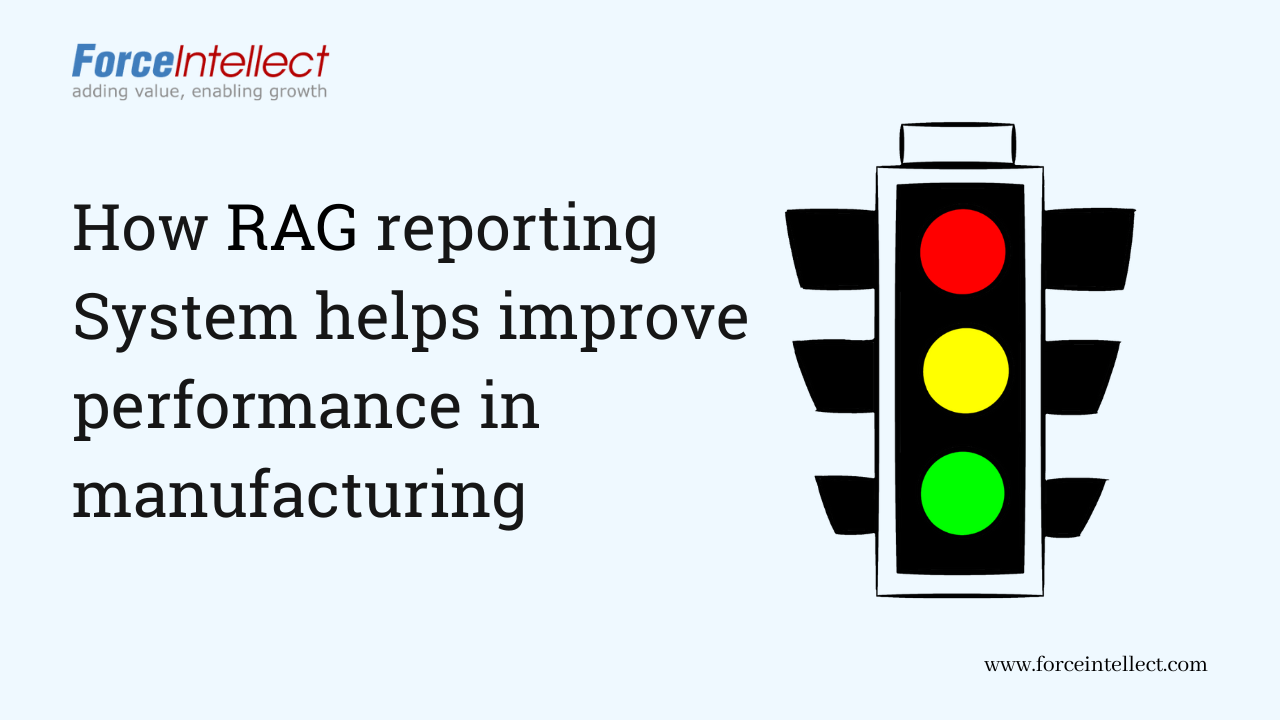
RAG reporting – How it enables performance improvement in manufacturing
RAG reporting is an effective way to monitor the performance of various areas of a manufacturing business such as purchase, inventory, production, quality, dispatch, payable, receivables, etc. It helps understand the effectiveness of each process and highlights areas that need immediate attention for continuous improvement.
In this article, we will learn what is RAG reporting system, why it is important in the manufacturing industry, how it is implemented, who can benefit from RAG Reporting & more
What is RAG reporting?
The RAG Reporting System is a visual method used to understand each process. RAG Reporting, uses the colours Red, Amber (or Yellow), and Green, to represent the status or performance against the key performance indicators (KPIs) defined. Each colour signifies a different level of performance:
Red Colour:
It indicates areas where performance is below the desired level, where there is high risk, and issues that require immediate attention. E.g. When actual production is lower than 50% of the target. Or, an order has been past due N days from the committed delivery date.
Amber (or Yellow) Colour:
It depicts areas where there is less risk, but a reason for caution or concern if not monitored regularly, similarly, performance is at an acceptable level but needs continuous monitoring to prevent problems. E.g. When actual production is 60%-70% of target. Or, a pending order which is about to reach or just passed its committed delivery date.
Green Colour:
It is used when the manufacturing processes are meeting or exceeding expectations of KPIs. E.g., A plant where production targets are consistently met or exceeded. Or, Orders are consistently delivered on time.
How to set up RAG reporting system in manufacturing?
Setting up the RAG reporting system properly is a crucial activity to ensure accurate reports that indicate areas of performance improvement
- Define Metrics: Define the key performance indicators (KPIs) you want to measure and report for each department such as purchase, sales, inventory, etc. E.g. financial performance, sales targets reached, inventory levels, etc.
- Specify Performance Parameters: Defining parameters means specifying a range of values to determine what is Red, Amber, or Green i.e the RAG status. Communicate the performance parameters to all concerned team members, so they know exactly how they are performing. E.g., For sales targets, you may set less than 50% as Red, between 51%-80% as Amber, and more than 80% as Green.
- Select Reporting Frequency: Determine how often to monitor the KPIs. E.g., some processes like inventory may need daily reporting, others may need weekly/monthly reporting, and so on. Define the same for each manufacturing process.
- Design Report Format: Prepare a report format that depicts the Key metrics along with their RAG status (Red, Amber, Green). This can be done in MS Word, ME Excel, or Dashboard, as per your needs. Make sure it is easily understandable so that every team adheres to using it.
- Responsibility: Specify the persons who will be responsible for generating RAG reports at specified intervals and for monitoring the metrics over some time. E.g. may be managers for each department.
- Regular Review for Continuous Improvement: Regularly review the RAG reports to identify areas that need urgent attention (Red), areas of caution (Amber) that may need monitoring or adjustment, and areas of success (Green) that can be maintained or built upon. Sometimes you may have to adjust the parameters defined depending on the performance.
Why use the RAG reporting in Manufacturing? What are the benefits?
The implementation of the RAG Reporting System offers several advantages for manufacturing companies:
- Simple: The colour coding in RAG reports provides a simple & clear picture of manufacturing performance. Makes it easy to identify areas that need attention.
- Timely Decisions: With regular monitoring and reporting, management can make timely decisions to allocate appropriate resources for addressing the problem areas.
- Proactive Risk Management: Since problem areas get highlighted early on, companies can prevent larger issues or avoid grave risks that can have a big impact on the company.
- Performance Tracking: RAG reports help understand trends and patterns that can enable process improvements and optimization efforts.
- Improves Efficiency: Continuous focus on performance improvements, leads to streamlined processes, improved efficiency, and reduced waste.
- Accountability for continuous improvement: RAG reporting indicates performance of each department and provides actionable insights for improvement. So, every team knows where it lacks and has to take ownership & accountability for achieving desired goals & performance levels.
Who should use the RAG reports in Manufacturing?
Stakeholders of various departments from a manufacturing company must leverage RAG reports to track and monitor performances. Example:
- Production Managers: Production managers must use RAG reports to monitor the performance of production lines, identify bottlenecks, and take corrective actions to maximize efficiency. E.g. Monitor metrics such as cycle time, downtime, yield rates, etc.
- Quality Managers: Quality assurance teams rely on RAG reports to monitor quality metrics and identify deviations from quality standards, enabling timely interventions to maintain product quality. E.g. Track metrics such as defect rates, rework percentages, customer complaints etc.
- Supply Chain Managers: Supply chain managers can use RAG reports to monitor supplier performance, delivery times, identify potential disruptions, and implement contingency plans to mitigate risks.
- Senior Management: Senior management usually must go through many reports to review and determine the status and health of the business functions. RAG reports can save a significant amount of time as management can focus on Red and Amber areas and devise strategies accordingly. E.g. Metrics related to production, finances, budget, quality etc.
How does ERP Software help implement RAG Reporting?
ERP (Enterprise Resource Planning) software can help implement RAG reporting more effectively due to the following reasons:
- Centralized Data Repository: ERP systems centralize data from various departments and functions, providing a single source of truth for RAG reporting metrics
- Data Collection: ERP helps gather data in digital format and in real-time from production, inventory, quality etc. This facilitates accurate data collection.
- Real-Time Monitoring: ERP provides dashboards and reporting tools to enable real-time monitoring of performance status across the organization.
- Implement Alerts and Notifications: with ERP software, companies can set up alerts and notifications when performance deviates from normal or falls into the Red or Amber zones.
- Automated Reporting: ERP helps prepare and schedule business reports for desired timelines, custom date ranges, and even schedules and sends reports to designated individuals as per the time specified. This enables regular reviews to identify trends, root causes, and areas for further optimization.
Summary
RAG reporting is valuable for tracking, monitoring, and improving manufacturing performance. By leveraging RAG report and RAG analysis, manufacturing organizations can streamline and optimize processes, improve productivity, and achieve greater efficiency.
See how Spectrum ERP can help implement RAG reporting.
Contact Us for more details