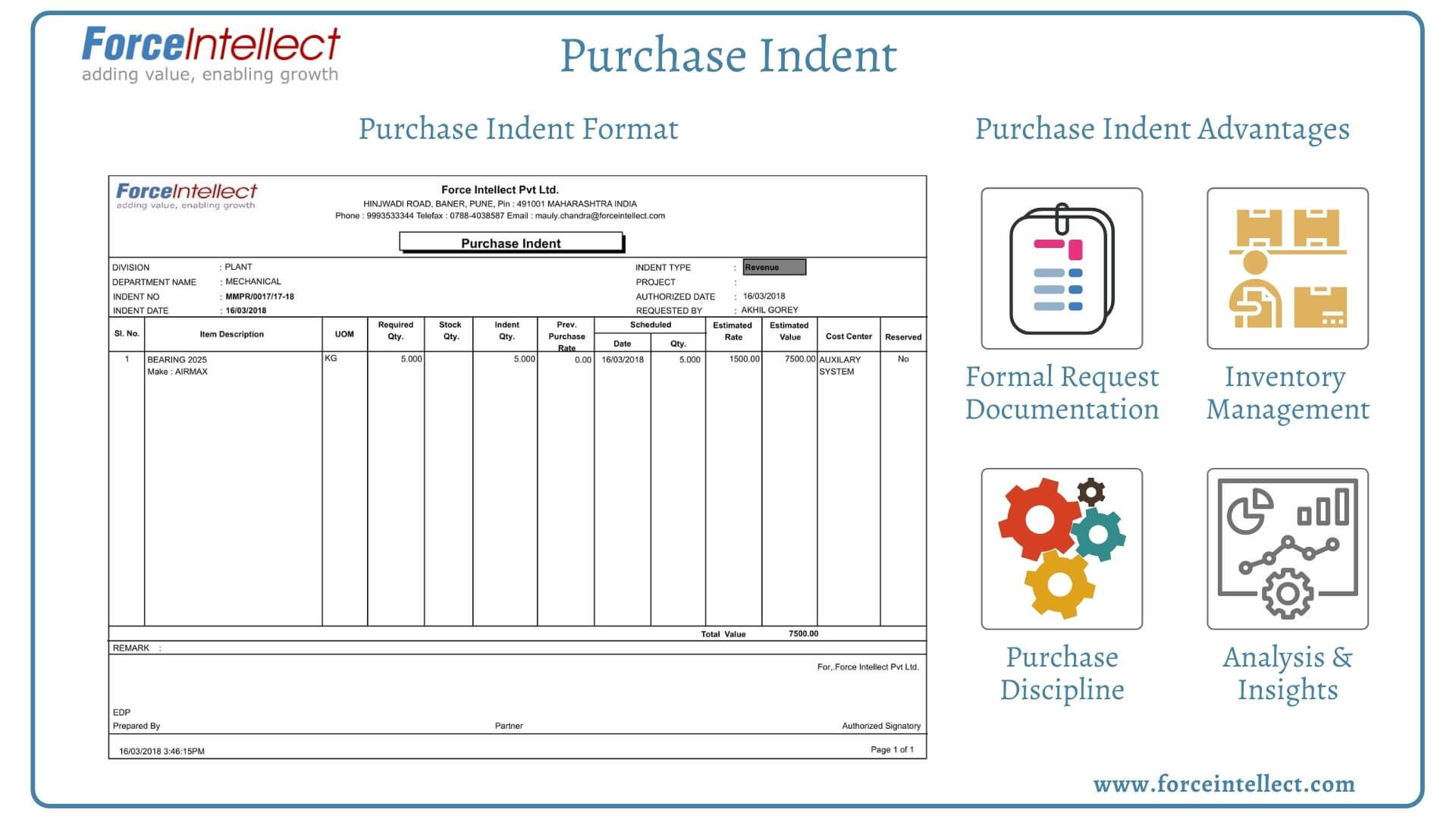
Purchase Indent | Purchase Indent Format
Purchase Indent presents a formal requisition for the purchase of items/materials needed by an organization. Creating a Purchase Indent & setting up a workflow for its approval are crucial elements in defining the purchase process of an organization.
What is the purchase process like in your organization? Do you have a defined workflow for purchase requisition? Do you create a Purchase Indent and approve it before creating a Purchase Order?
In this article, we will cover the following topics :
- What is a purchase Indent?
- Why the need for a Purchase Indent?
- What does the Purchase Indent Format look like?
- What Information is included in the Purchase Indent?
- What are the benefits of Generating Purchase Indent via ERP Software?
What is a Purchase Indent ?
Purchase Indent is an internal document used by companies to authorize the requisition of purchase of raw materials, consumables, capital items, etc. needed by the company. Purchase requisition is usually prepared by the store-in-charge for the replenishment of stocks or by end-users of the department for new requirements. It provides detailed information about :
- Item Name with the make, technical description, quality specifications, for acquiring right materials
- Required quantity along with the unit of measurement (Tons, Kgs, Litre)
- Required by date and whether it is required in one lot or staggered over time
- Estimated prices may also be mentioned to budget the requirement
After Purchase Indent is prepared, it is forwarded to concerned approvers; one or many depending on the process of each company; as well as the value of the purchase indent. Usually, relevant department users, stores department, finance authorities, management representatives are involved in the approval of a Purchase Indent. Only when it is validated and approved by the concerned authorities, it is sanctioned for creating a Purchase Order.
Why the need for a Purchase Indent?
1. Formal Request & Documentation
Purchase Indent or Purchase requisition provides all details about the items required, make, specifications, units, expected date, estimated prices, etc. When all this is formally documented and agreed upon, it helps provide complete clarity and ensures that everyone agrees that the right materials are being ordered as per specific requirements. This eliminates the chances of misunderstanding and pointing fingers at others within the company. This ensures the right material is available in the required quantity at the appropriate time.
2. Inventory Management
When separate Indents are raised for every purchase request, companies have complete documentation of quantity in hand and required quantity along with the estimated price, warehouse location, required date, and so on. This makes inventory management easier.
Purchase Indent can also be raised while being linked with Bill of Materials, Production Planning, Plant Maintenance activities, Stock Reorder Levels, etc. This reduces chances of human errors, or mismanagement and ensures that items are purchased when they are required for actual consumption, and helps prevent situations of overstocking.
3. Purchase Discipline
Purchase is a crucial activity for every company. At the same time, mismanagement of purchases can have serious consequences such as overstocking of materials or shortage of materials required in production.
Purchase Indent helps imbibe a culture of planning purchases in advance to ensure availability of material on time as well as keeps a check on ad-hoc purchases. This is also helpful when the prices of items are market controlled and fluctuate daily.
Purchase Indents approvals via the proper channel ensures review of the purchase and that purchase discipline is being followed in the company.
4. Analysis & Insights
Tracking Purchase Indents history provides insights that help companies determine how disciplined the users are; in planning their purchases, how often the Indents are being raised, how much time is available to the purchasing team to negotiate and find a better deal.
This explains how organized or how well material requirement activities are being performed, whether they are aggregating indents to avail benefit of bulk purchases or not, and whether the company gets enough time to purchase at optimum prices or not. This helps to take corrective measures as required. Thus, purchase indents provide important inputs in establishing material requirement practices within an organization.
What does the Purchase Indent look like?
Purchase Indent can be prepared in hard copy in Word Format or Excel Format, or prepared as online forms via ERP and a soft copy can be sent to various approvers online via Email/SMS
Download : Purchase Indent Excel Format
Sample Purchase Indent Format
What Information is included in the Purchase Indent?
The information contained in a Purchase Indent can be classified into 2 categories. First is the information about the Indent itself – that includes number, date, type, requested by, created by, authorization date, and so on. The second part covers the detailed and clear specifications of the purchase request. Let us look at each one.
Information about the Indent
- Indent Number: Unique Identifier for every Purchase Indent created within the organization. This helps keep a check of all the indents being raised within the organization.
- Indent date: Specifies the Indent Creation Date. This helps to determine how long it takes from raising an Indent to the approval of indent and purchase order generation.
- Indent Type: This mentions whether purchase pertains to raw material, consumables, assets, etc. This helps to determine the appropriate treatment and activities for Indents such as Revenue Indent, Capital Indent, Proprietary Indent for respective purchases.
- Requested By: Name of the person who prepares the Indent. If the approvers want to discuss any specific details before approval, they can directly speak with him/her. Accordingly, they can suggest modifications, approve with detailed notes or partially approve, etc.
- Department / Division: Specifies the department/division that is raising the request and will bear the cost of the purchases for internal accounting purposes
- Indent Approval Date: This specifies the date when the Indent gets approved by all. This helps to determine the number of days required for approval of indent. If approval is quick, the purchasing team will get more time to purchase at the optimum price.
Information about the Items to be Purchased
- Item Description: Provides precise information of the items to be purchased along with the make, technical details, quality specifications, etc. Providing perfect item/material description ensures the right purchases.
- Unit of Measurement: Whether the unit of measurement is Meters, Liters, Kilograms, Tons, etc.
Required Quantity: Specifies the amount of quantity required E.g. 5000 bags of cement. - Stock Quantity: Specifies How much stock of the same is currently available. Provides insights on whether they should approve or delay the purchase depending on the urgency.
- Previous Purchase Rate: This information is useful for comparison of previous and current purchase prices, as well as estimation purposes.
- Schedules Date & Quantity: This will be a single date if all quantity is to be delivered in one go. E.g. 5000 bags to be delivered by 10 Jan. However, scheduled dates will have to be specified if deliveries are spread over some time. E.g. 1500 bags to be delivered on 10 Jan, 20 Jan, 30 Jan & 500 bags on 10 Feb
- Estimated Rate & Value: Mentioned for estimation purposes & budgeting of expenses.
- Cost Center: Mentions a specific cost center that requires the items/material. E.g. In the case of a Production shop, they may specify, that material is being acquired for which specific machine.
- Reserved: Specifies whether these items are being purchased for a specific purpose and reserved for a cost center and others should not have access to it.
- Remarks: Indenters can specify suggestions, remarks for particular items/materials being requisitioned.
What are the benefits of generating Purchase Indent via ERP?
With the help of ERP Software, a lot of activities relating to Purchase Indent can be automated. It saves a significant amount of time, and effort and also makes the entire process from raising the indent to the receipt of goods completely traceable and auditable.
1. Digital Documentation of Item/Material Request
With ERP you can create Purchase Indent online, save and share them quickly and easily with attachments, documents regarding items/materials required, make, specifications, units, expected date, estimated prices, notes about approvals in digital format.
ERP makes it easier to edit/modify/resubmit the indent. Once digitized, you can gain various benefits such as checking progress, generating reports, based on various parameters, to gain insights and share with concerned people easily.
2. Buying Discipline
Companies use purchase indents to implement buying discipline. With help of ERP, companies can define limits on purchasing value or quantity for a specific period. E.g. In the case of Stationary, need approvals for purchase request only if more than 10000 pages per month are to be purchased. Or stop purchase transactions if the total value reaches Rs. 1 Crore for a particular project. With ERP, companies can send notifications when the threshold is nearing and stop transactions as well.
3. Approval Workflow & E-Approvals
ERP helps define purchase indent approving authorities from each department. You can set up a single approver or multiple levels of approvals depending on purchase order value/amount.
ERP sends automatic Emails/SMS for online approval to respective people from each department when the indent is raised.
4. Real-Time Tracking
ERP enables real-time tracking of purchase indent status. It sends auto-reminders if approval is pending for a certain amount of time. This ensures timely action is taken and avoids delays in the process. Users can also track progress.
5. History & Trends
With purchase indent history gathered over some time, it provides insights into material requirement trends. This helps identify if a particular item is being requested frequently or a particular machine requires more materials and so on. This helps to take corrective actions such as checking wastage of material or improving maintenance of plants machinery etc. as required.
Summary
Purchase Indent is a formal document to authorize the requisition of materials for creating a purchase order. It can be prepared online via ERP or in Word Format or Excel Format. It is a crucial document that helps manage inventory better and establish material requirement discipline within an organization. If proper purchase indent practices are followed it will help curb mismanagement and save the working capital of the company.
Read more about our Material Management Solution here.
Read more about Spectrum ERP Software & Request a Demo Now.
Contact Us for more information.