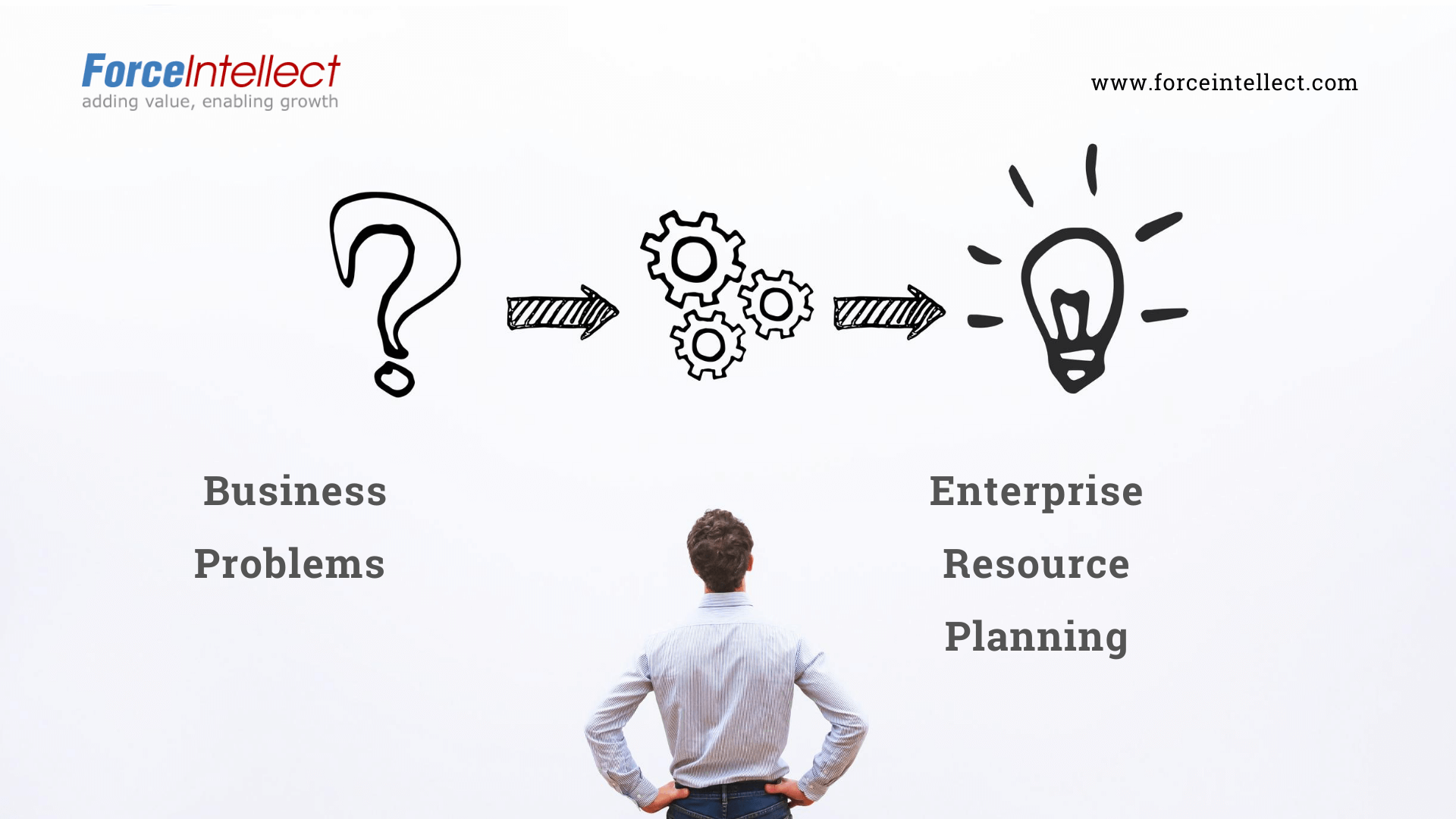
Facing Business Problems? See How ERP Can Solve Them
As manufacturing SME, do you face any problems in day to day operations? Do you find it difficult to make informed decisions? Are there any specific business areas you find bottlenecks in? or Areas you would like to improve? Do you have complete visibility of your business? Have you given a thought on how an ERP solves business problems?
We have come across many companies that do not take advantage of digital technology adoption and ERP implementation. While others accept technology after they face major business problems that require them to change.
Let me share some examples with you:
This manufacturing SME had 2 different manufacturing locations. The departments were carrying on their own activities like procurement, inventory planning, and so on. Each department was storing and sharing all information using word files, excel sheets, etc. The employees had to do a lot of duplicate work, reconciliations, and repetitive follow up to ensure that the records were up to date. However, there were still chances of errors due to omission. This is an example of a Lack of Single Source of Accurate Data
One company ran out of stock of a commonly used bearing. It took this company, almost 12 hours to arrange the right bearing and they had to pay a hefty price in terms of loss of production & idle manpower. This is a typical scenario when standard business practices are not defined & documented.
In another company due to poor material management practices, they had piled up a lot of surplus stock. Effectively, a lot of working capital was blocked in inventory and they were finding it difficult to carry out their day to day expenses also. This depicts a lack of inventory management practices & good inventory control.
One manufacturing company was regularly losing orders and facing stiff competition despite quoting with the lowest possible margins. Upon careful investigation, they found that every department was adding an extra margin of safety. This is another example of a lack of best practices & improper communication in the organization.
Have you faced similar business problems? Do you notice similar patterns in your company?
In the following sections, we will share details of common problems faced by manufacturing SMEs and how to overcome these business problems with ERP Software. When you become aware of how ERP can solve business problems you will be able to take a confident step forward towards ERP implementation.
Common Business Problems faced by Manufacturing SMEs
Let us now understand the common business problems faced by small businesses and manufacturing SMEs.
1. Absence of Single Source of Data:
Companies’ data is stored in silos by each department & location. They do not have a single source of data. If they need to create any reports or analyze data, they have to look into multiple systems, to collate all the information.
2. Lack of Real-Time Accurate Data
Companies cannot gather real-time data from employees on the shop floor, in the warehouse, field service technicians, salespersons, etc. They have to wait until they return to the office and update the spreadsheets or manual systems. So, data is never 100% complete and correct.
3. Reporting Challenges
Employees of companies managing information on spreadsheets have to spend a lot of time, reconciling data for every department, location in order to present the most accurate data. This is very time consuming & requires a lot of follow up & coordination and is person dependent. Moreover, there are possibilities of human errors & errors of omission.
4. Lack of Standard Processes & Business Discipline
Being spread over locations or not having control over the entire business processes makes it difficult to establish company-wide policies, standard business processes, and implement rules for business & financial discipline.
In one of the above examples, if the company had set up standard processes for inventory management and implemented discipline for inventory control, defined when to reorder inventory, triggered an alert for purchase, the stock out situation could have been avoided.
5. Lack of Right Information to Right People at Right Time
When there are no systems in place, information is not present in a single location, it is time-consuming to coordinate with various departments & keep every department appropriately informed. In such a situation, concerned people cannot take appropriate actions or timely measures to mitigate risks.
6. Low Productivity
It is often observed that when there are no standard processes, no business discipline, lack of proper information, it results in less than optimum utilization of resources, wastage, lower productivity. In the earlier example, information that stocks were about to get over was not available. This resulted in 12 hours downtime, manpower remained idle, machinery was not utilized and the entire batch was delayed.
7. Communication Challenges & Delays in Approvals
When manual processes & paperwork is being followed, communication is person dependent. It takes time & effort for meetings, follow-ups & approvals. The absence of a single person may delay the process of approvals/decisions.
8. Lack of Data-Driven & Analysis Culture
Without proper systems in place, it is difficult to keep a track of the trends, identify the patterns, and make proper data-backed informed decisions.
How ERP Solves business problems?
1. ERP provides Single Source of Real-Time Accurate Data:
Implementing an ERP creates the digital backbone for the company. ERP captures data in digital format, integrates information from multiple locations, processes & systems, saves it in a single database, and makes it easily accessible anytime, from anywhere. Mobile Apps provide access to ERP data & facility to enter real-time data into the ERP directly from the field. Thus, ERP creates a single source of real-time and accurate data for understanding trends and analysis. It also brings transparency in business processes.
2. ERP enables implementing Standard Processes & Business Discipline
ERP software helps you define company-level policies, to be followed by all departments, functions, processes. ERP facilitates rolling out standard processes & business disciplines across locations. You can define and implement business flow, rules & guidelines, validations, and checks, approval workflows, set up notifications & alerts for Production, Procurement, Inventory, Sales, Plant Maintenance, and so on.
3. ERP Digitizes Automates Tasks & Improves Communication Collaboration
ERP digitizes, automates manual, repetitive tasks, follow-ups, approvals. ERP establishes proper information workflow between people and processes, and systems. It also allows you to define rules for managing by exception. ERP helps create job roles & hierarchies to ensure the right information is provided to the right people. You can send SMS & Email Alerts, at run time and allow concerned stakeholders to make decisions on the Go. ERP even provides reminders for pending actions. All this improves communication and collaboration across departments and locations and speeds up the approvals process.
4. Easy Accurate, Real-Time Reporting with Detailed Trends & Analysis
ERP helps define Key Performance Indictors (KPIs) for every function such as procurement, inventory, quality, sales, finance, and so on. ERP makes it easy to generate reports by entering the right queries and parameters. This saves a significant amount of time & provides accurate reports. Business Intelligence tools & analysis provide deep insights into every aspect of a business. Stakeholders can discuss facts & figures from every department and monitor the performance based on department-wise reports published weekly or monthly as required. This helps establish a culture of making data-driven informed & timely decisions.
Summary
Implementing ERP Software is an effective means to conquer business problems. You will be able to achieve a single source of accurate data, establish standard processes & disciplines, achieve effective communication & coordination among teams, build a data-driven culture. All these will help your company to scale & grow.
Want to know how ERP can solve your business problems? Request a DEMO of Spectrum ERP