How inventory optimization can be done with IT/ Role of Technology in Inventory Management
Inventory has always been a cause for concern for most of the business. Whether you should always be prepared with stocks in your inventory but face the risk of stock deterioration or you just have enough stocks in your inventory to fulfill your orders(also called just-in-time delivery) but face the risk of total debacle in case of some unforeseen disaster like natural disasters, terrorist attack or a labor strike. So which one should you go for?
There is no exact answer to this question you can either play it safe or live on the edge and maximize profits. To maximize your profits while being prepared for disasters needs people with skills and imagination. If you go for the latter one role of technology in inventory management will be evident. To understand this more clearly let’s see how dell faced an unforeseen disaster.
How Dell used IT in inventory in time of emergency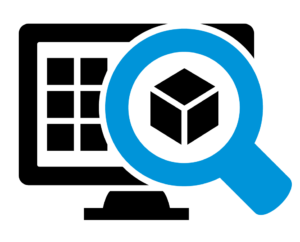
We know that Dell created a system where they let people order the specific specification of PC and made it after they got the order. In this way, they only had stocks of PC that are already sold hence they faced minimum to no loss due to deteriorating of stocks in the inventory. They were close to reaching the ideal zero in their inventory i.e. they had almost zero inventory that maximized cash flow but in 2002 a 10-day labor lockout idled 10,000 union dockworkers, shut down 29 West Coast ports extending from Los Angeles to Seattle, and blocked hundreds of cargo ships from unloading the raw materials and finished goods that fuel U.S. commerce. The port closings paralyzed global supply chains, bloodied retailers, and manufacturers, and ultimately cost U.S. consumers and businesses billions.
It was expected that with Dell’s inventory model this lockout will hit them hard. Without warehouses filled with motherboards and hard drives, everyone figured that the world’s largest PC maker would simply find itself with nothing to sell within a matter of days but Dell was in constant, round-the-clock communication with its parts makers in Taiwan, China, and Malaysia, and its U.S.-based shipping partners, who alerted it to the possibility of a lockout some six months before it occurred. They dispatched a “tiger team” of 10 logistics specialists to Long Beach, California, and other ports; they worked hand in hand with Dell’s carrying and freight-forwarding networks to assemble a contingency plan. When the tiger team confirmed that the closings were all but certain, Dell moved into high gear.
It chartered 18 747s from UPS, Northwest Airlines, China Airlines, and other carriers. A 747 holds the equivalent of 10 tractor-trailers — enough parts to manufacture 10,000 PCs. Moreover, Dell worked with its Asia-based suppliers to ensure that its parts were always at the Shanghai and Taipei airports in time for its returning charters to land, reload, refuel, and take off. The company was consistently able to get its planes to the United States and back within 33 hours, which kept its costs down and its supply chain moving. In Asia, freight specialists saw that Dell’s parts were the last to be loaded onto each cargo ship so they’d be unloaded first when the ship hit the West Coast. The biggest test came when the ports reopened and companies scrambled to sort through the mess of thousands of backed-up containers. Tiger team had anticipated this logistical nightmare. Even though Dell had PC components in hundreds of containers on 50 ships, it knew the exact moment when each would be cycled through the harbor, and it was among the first to unload its parts and speed them to its factories in Austin and Nashville. In the end, Dell did the impossible: It survived a 10-day supply-chain blackout with roughly 72 hours of inventory, and it never delayed a customer order.
The aftershocks of the port closings reverberated for weeks. Many companies began to question the wisdom of running so lean in an uncertain world, and demand for warehouse space soared as they piled up buffer inventory to ensure against labor unrest, natural disasters, and terrorist attacks. But for Dell, the episode only reinforced the value of living on the knife’s edge.
So should a business use Technology for Inventory Optimization?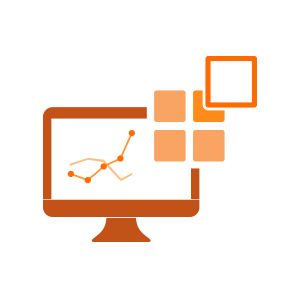
The case of dell showed us that even in the time of crisis dell kept its calm and used IT in the best possible way to come up with a solution that kept its inventory going. Just-in-time inventory comes with many benefits best one being that you never have to worry about stocks in the inventory deteriorating and if the model is used shrewdly with IT the shortcomings of the model can also be covered as seen in the case of dell.